lieuz
Chumono
I wanted to share this year-long journey so that I can say to myself that I did it, and also so that others can observe and maybe not attempt this because, in the end, it'll probably be better to just go and buy a pot for an astronomical amount of LESS effort. I've been trying to come up with ways to replicate a pot I've made. Even before all of that, I came across this video I'm sure many have probably seen.
This one video when I watched it, was immediately captivated. I dabble in ceramics and found great joy when creating various pots; however, something about replication just entranced me.
Our club offered a crash course into bonsai pot making and that was pretty much the start of everything for me. I did the whole pinch pot, slab building, and wheel-thrown pots and they were all very entertaining bonsai-related offshoots of things to do during the winter.
After building this unique pot, I had the motivation to want to replicate it.
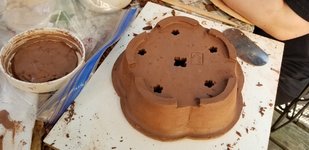
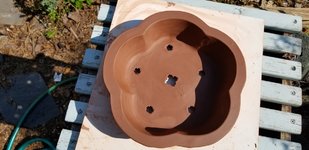
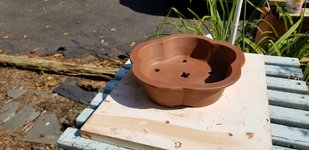
This was a pretty clean build, everything was well defined, it was crisp and it was unique. In hindsight, this was a fairly ambitious pot to try to replicate.
I think I spent a pretty good amount of time devising a plan on how to approach coming up with a mold that would allow me to replicate the pot, but still allowed me the option to customize (feet). In April of 2021, I just dove head first into it.
A base was poured first so the pot can stand atop something.
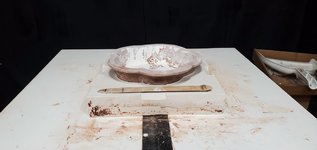
After pouring the second layer, the registration marks were made and the pot was able to release from the plaster thanks to Murphy's Soap.
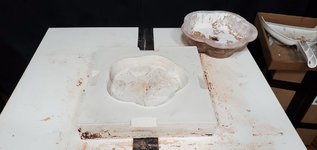
There was an unforeseen issue with the plaster not flowing underneath the pot. This made for mounds of plaster.
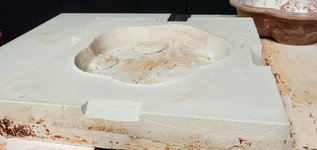
Ultimately, I'll have to backfill with plaster so I can make the feet from scratch.
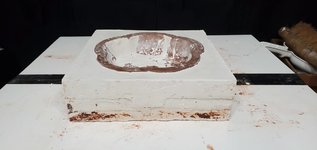
The third layer was to fill it up to the lip. In hindsight, this later was pretty important. In fact, the entire pot should have been casted upside down. There were a lot of unevenness and that will eventually be a huge problem.
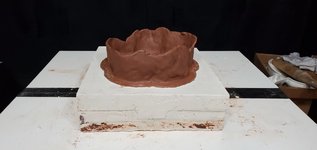
I have to make the last layer which is the top, The top should be like the first layer, it should not have any imprint on it. It should just flatten the clay so that excess can be removed.
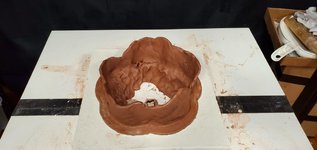
It didn't occur to me how important it was that this layer should be impeccably smooth; however, it isn't.
This one video when I watched it, was immediately captivated. I dabble in ceramics and found great joy when creating various pots; however, something about replication just entranced me.
Our club offered a crash course into bonsai pot making and that was pretty much the start of everything for me. I did the whole pinch pot, slab building, and wheel-thrown pots and they were all very entertaining bonsai-related offshoots of things to do during the winter.
After building this unique pot, I had the motivation to want to replicate it.
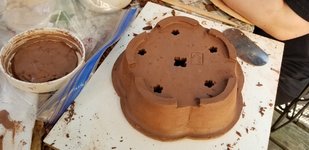
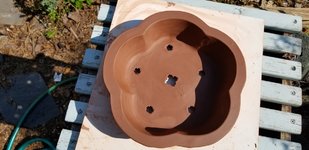
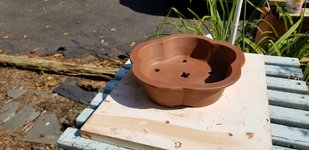
This was a pretty clean build, everything was well defined, it was crisp and it was unique. In hindsight, this was a fairly ambitious pot to try to replicate.
I think I spent a pretty good amount of time devising a plan on how to approach coming up with a mold that would allow me to replicate the pot, but still allowed me the option to customize (feet). In April of 2021, I just dove head first into it.

A base was poured first so the pot can stand atop something.
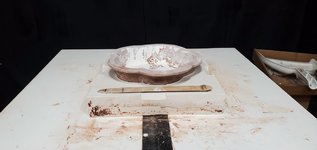
After pouring the second layer, the registration marks were made and the pot was able to release from the plaster thanks to Murphy's Soap.
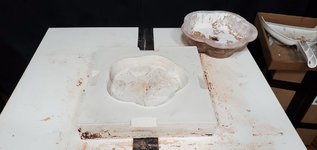
There was an unforeseen issue with the plaster not flowing underneath the pot. This made for mounds of plaster.
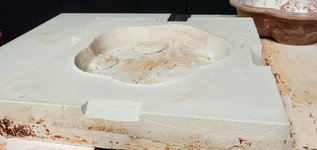
Ultimately, I'll have to backfill with plaster so I can make the feet from scratch.
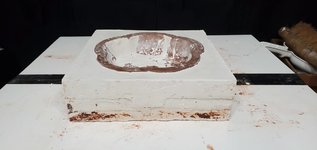
The third layer was to fill it up to the lip. In hindsight, this later was pretty important. In fact, the entire pot should have been casted upside down. There were a lot of unevenness and that will eventually be a huge problem.
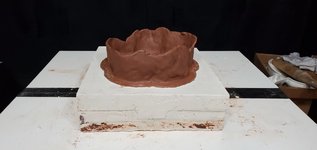
I have to make the last layer which is the top, The top should be like the first layer, it should not have any imprint on it. It should just flatten the clay so that excess can be removed.
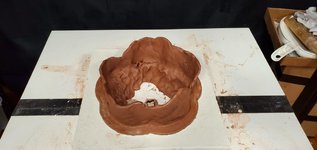
It didn't occur to me how important it was that this layer should be impeccably smooth; however, it isn't.