Hartinez
Masterpiece
Work has been slow at the start of this year and so I decided to make a new stand. My grandpa passed away this last year and before he did he sent with my mom 2 pieces of what he was calling Mahogany (which I know @Bonsai Nut is a complicated topic of conversation in the wood world). Regardless, the boards were awfully wide. About 16” or so.
They both needed flattening and were too wide for my thickness planer. I used a router sled and flattening bit to get them dialed in. The joinery and subsequent curve at the joinery is a trick I learned from Austin Heitzman. I cut the 27.5 degree angles first then go back through with a rather large cove bit to achieve a heavy round over where the joints meet. The angle has to be cut first then the rounding.
The live edge portion is a piece of Russian olive I picked up from my local exotic wood shop. I thought the color complimented the mahogany nicely. Each side has a different section of the live edge giving two different possible fronts for the stand.
It’s a rather large stand and could host a number of tree types from deciduous to conifer. Overall top dimension is about 15”x20” with a height of about 6”.
I’m pleased with how it turned out. It’s def for sale so if anyone is interested reach out. I’m also going to post to Instagram and subsequently the FB auctions. I’ve often not charged enough for stand in the past but will def be asking for this stands worth. If I don’t sell it though, I’ll have a sweet stand to use for my own trees!
Thanks for looking!
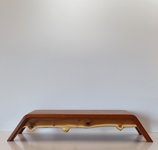
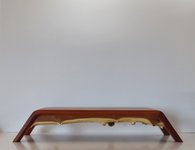
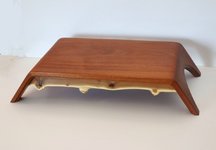
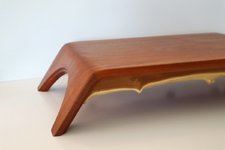
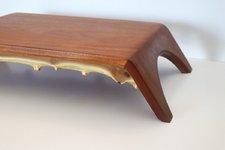
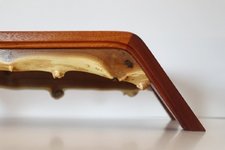
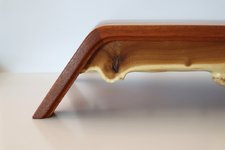
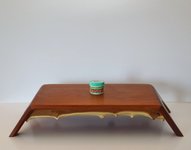
They both needed flattening and were too wide for my thickness planer. I used a router sled and flattening bit to get them dialed in. The joinery and subsequent curve at the joinery is a trick I learned from Austin Heitzman. I cut the 27.5 degree angles first then go back through with a rather large cove bit to achieve a heavy round over where the joints meet. The angle has to be cut first then the rounding.
The live edge portion is a piece of Russian olive I picked up from my local exotic wood shop. I thought the color complimented the mahogany nicely. Each side has a different section of the live edge giving two different possible fronts for the stand.
It’s a rather large stand and could host a number of tree types from deciduous to conifer. Overall top dimension is about 15”x20” with a height of about 6”.
I’m pleased with how it turned out. It’s def for sale so if anyone is interested reach out. I’m also going to post to Instagram and subsequently the FB auctions. I’ve often not charged enough for stand in the past but will def be asking for this stands worth. If I don’t sell it though, I’ll have a sweet stand to use for my own trees!
Thanks for looking!
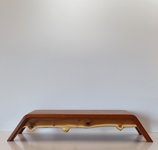
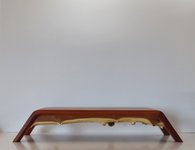
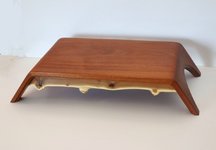
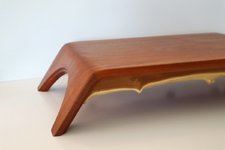
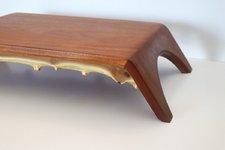
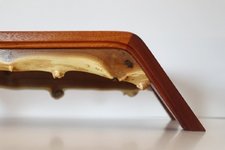
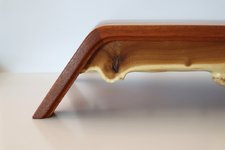
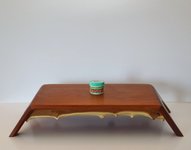