DonielDoom
Mame
Hey all!
Semi-recently I threw some attention towards making my own pottery. As I'm a bit intimidated by the complexities of the fired-clay process, namely the glazing and firing aspects, I opted to try something that seemed more forgiving or 'entry level'. This landed me with a bag of portland cement and some sand, among other things. A crude wheel from a lazy susan bearing, some wood, and a sawhorse would round things out.
I've made about a dozen at this point and think I've got some pretty neat designs and a lot to work on for the level of quality I seek. I think I could really get into this kind of thing... Regardless, I'm enjoying the process and have been learning a ton!
Anyways... I figured I'd get some feedback and share a bit. Let me know what you think and what you'd enjoy seeing. I'll keep throwing my project pics up until I get to current.
Here's Cement Pot #1!
Fully cured

Fully cured

Fully cured

Fully cured

Freshly thrown

Day after being thrown
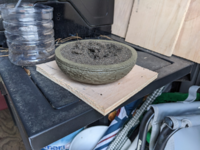
Day after being thrown

Semi-recently I threw some attention towards making my own pottery. As I'm a bit intimidated by the complexities of the fired-clay process, namely the glazing and firing aspects, I opted to try something that seemed more forgiving or 'entry level'. This landed me with a bag of portland cement and some sand, among other things. A crude wheel from a lazy susan bearing, some wood, and a sawhorse would round things out.
I've made about a dozen at this point and think I've got some pretty neat designs and a lot to work on for the level of quality I seek. I think I could really get into this kind of thing... Regardless, I'm enjoying the process and have been learning a ton!
Anyways... I figured I'd get some feedback and share a bit. Let me know what you think and what you'd enjoy seeing. I'll keep throwing my project pics up until I get to current.
Here's Cement Pot #1!
Fully cured

Fully cured

Fully cured

Fully cured

Freshly thrown

Day after being thrown
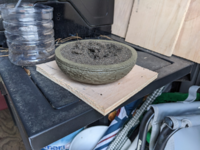
Day after being thrown
