ForrestW
Mame
This is kind of a long post/ series of posts– mostly for potters but anyone who is curious about bigger pots/bigger kilns feel free to read on. (note– bigger for an electric kiln– gas kilns and especially wood kilns are often MUCH bigger.)
My ceramic journey has been a little over 20 years now and it's ever evolving. Currently I am still a full time Art Teacher, and so my studio time can come in spurts. Over the last few years I have been trying to increase the size of pots I can make and that has involved obtaining or making a variety of things such as very large throwing bats, (which attach to the wheel head to allow more space) large foam boards and sheetrock boards that will stay nice and flat while working on the pots. You need a strong wheel– the wider you expand the bat the more torque it puts on the motor of the wheel. I have an older Brent CXC wheel that is rated to center 100 lbs. of clay, but it will struggle at times working the clay on the outer parts of my large bats. I currently have a nice 24” slab roller, pug mill to recycle clay and extrude 2” coils and a typical extruder I use for my feet and the coils I put where I attach the slab to the wall. All of those allowed me to get up to 26” pots but the kiln was the limiting factor.
This past year I started looking online for a used kiln that would allow me to expand my size. I currently have a 28”x 18” electric kiln, a 28” x 27” electric kiln (both L&L my preferred multizone kiln) and I built a Hybrid Gas, Wood kiln I can fire solo and I built it for Crossdraft Soda firing. (My other body of work) Sadly when I built that one I was doing a different genre of work and it's not ideal for bonsai pots– the downdraft gets much more even temperatures but less pronounced effect from the soda glaze. That one has a wear chamber of 27” x 27” x 32” tall.
This past fall I found a used kiln that was advertised as the Olympic 3027 which has an oval wear chamber of 42” x 30” x 29” and was only about 2 hours away. There were no pictures as the kiln was stored deep in a storage trailer and the owner was not able to unload it herself. She had an invoice from 2018 where she took that kiln into Olympic and had some brick repair, new elements, and a new control box– as well as fixing the lid hardwear.
So I went there with my trailer to take a look. It had never been used since it was fixed by Olympic but many of the bricks were damaged badly when she packed it into the moving trailer. It was missing some wires to connect the box, no stand, or lid hardware or shelves, but it was a decent price and So I decided to try and finish the repairs myself.
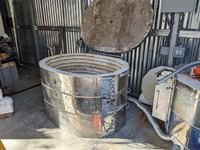

My ceramic journey has been a little over 20 years now and it's ever evolving. Currently I am still a full time Art Teacher, and so my studio time can come in spurts. Over the last few years I have been trying to increase the size of pots I can make and that has involved obtaining or making a variety of things such as very large throwing bats, (which attach to the wheel head to allow more space) large foam boards and sheetrock boards that will stay nice and flat while working on the pots. You need a strong wheel– the wider you expand the bat the more torque it puts on the motor of the wheel. I have an older Brent CXC wheel that is rated to center 100 lbs. of clay, but it will struggle at times working the clay on the outer parts of my large bats. I currently have a nice 24” slab roller, pug mill to recycle clay and extrude 2” coils and a typical extruder I use for my feet and the coils I put where I attach the slab to the wall. All of those allowed me to get up to 26” pots but the kiln was the limiting factor.
This past year I started looking online for a used kiln that would allow me to expand my size. I currently have a 28”x 18” electric kiln, a 28” x 27” electric kiln (both L&L my preferred multizone kiln) and I built a Hybrid Gas, Wood kiln I can fire solo and I built it for Crossdraft Soda firing. (My other body of work) Sadly when I built that one I was doing a different genre of work and it's not ideal for bonsai pots– the downdraft gets much more even temperatures but less pronounced effect from the soda glaze. That one has a wear chamber of 27” x 27” x 32” tall.
This past fall I found a used kiln that was advertised as the Olympic 3027 which has an oval wear chamber of 42” x 30” x 29” and was only about 2 hours away. There were no pictures as the kiln was stored deep in a storage trailer and the owner was not able to unload it herself. She had an invoice from 2018 where she took that kiln into Olympic and had some brick repair, new elements, and a new control box– as well as fixing the lid hardwear.
So I went there with my trailer to take a look. It had never been used since it was fixed by Olympic but many of the bricks were damaged badly when she packed it into the moving trailer. It was missing some wires to connect the box, no stand, or lid hardware or shelves, but it was a decent price and So I decided to try and finish the repairs myself.
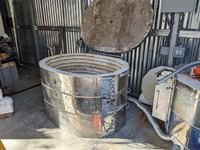
